2016 – What an eventful year for Infrakit
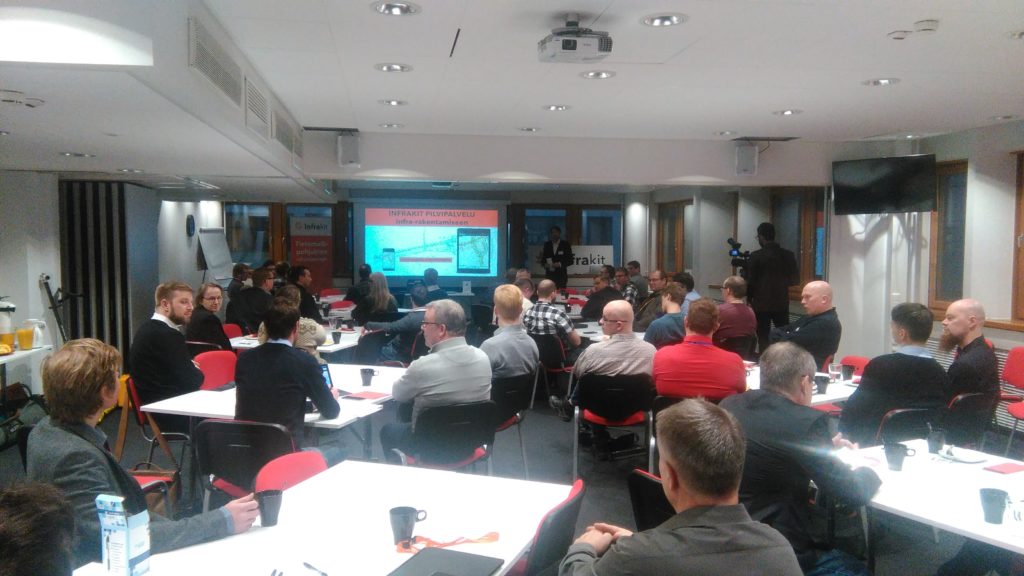
2016 – What an eventful year for Infrakit
Only thinking about last year makes me a little dizzy. We organized so many of our own events and participated into even more! I thought it would be nice to take a trip down the 2016 memory lane by going through some of those events.
Infrakit Day Helsinki
This is the main event for us where we invite our customers; Infrakit super users and beginners, industry influencers, and our partners etc. The main purpose for Infrakit Day is to bring guests from all sectors of infrastructure industry together — project owners, designers, contractors, surveying and GPS equipment manufacturers. And the purpose came through, when at the event our guests were exactly that – a great mix of all.
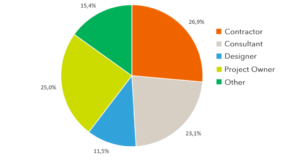
Participants’ sectors counted from all 3 Infrakit events
What was also very nice, was the wide scale of participants’ roles: everything from CEOs to worksite engineers to head of designers. This was later said to be the thing that differentiated our event from similar ones: people got to talk with everyone – from each sector, role and Infrakit user level. Learning from others was key!
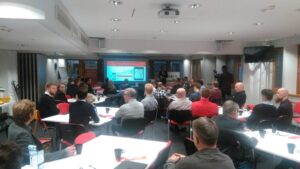
A great turn-out for Helsinki’s Infrakit Day.
And talking about learning, we managed to get some great speakers to tell us all about their cases and problems vs. solutions in the digitalizing industry. Through an after-event survey we received some feedback that the quality of presentations was great, but the program itself became quite heavy as there were so many speakers. Well, we learned from that and booked fewer presentations for the future events to give some room for digesting the information and discussing it with others. Finding the perfect balance is a challenge, but an interesting one!
Infrakit Days in Oulu and Kuopio
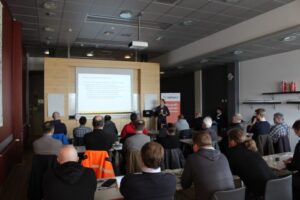
Infrakit Day in Oulu
There was a demand for having more of these events, so we made it into a small roadshow! We realize that most of our customers are outside of Helsinki, so we went to them. The positive feedback we got from both cities’ events revolved around interesting and informative topics, and enabling valuable discussion among peers and between all parties. The constructive criticism we got from Oulu was that there wasn’t a presentation from a worksite point of view – foreman for example – and it could be nice to start the event with a round of introductions. In Kuopio our guests told us, Infrakit team, to talk more about our own product and services. Will do for next one!
You can read further blog posts with all event PPT slides from here (only in Finnish): Infrakit-päivä 2016 (Helsinki), Infrakit-päivä Oulussa, Kuopion oma Infrakit-päivä.
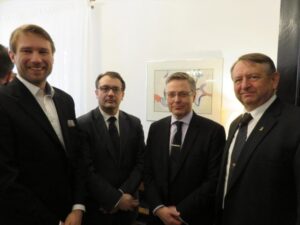
CEO Mr. Kivimäki, State Secretary Trifunovic, Ambassador and State Secretary Kern
Serbian Infrakit Day
Our Serbian office held their own event in Belgrade in association with the Embassy of Finland. I heard it was a success for they had 50 people invited and enrolled, but 70 people showed up. What a positive problem! The event programme, speakers, and guests were in line with the Finnish ones. I was happy to hear there was a lot of discussion about the digital infra-industry during and after the event. You can read the English blog post about it here: Belgrade’s Infrakit Day.
Infrakit Reseller Event
As Infrakit is expanding its business globally, resellers come into play. During 2016, and even earlier, we had some interesting talks about how we could work together with companies that – like us – are in the crossroads of the industry, who see that infra-industry is digitalizing fast and who would be happy to be involved in making the digital leap easier for everyone. This in mind we invited the key people in some companies around the world to the deep forests in Finland in October. And we made them run in the pitch black forest with Infrakit as GPS – a fun game we called Infrakit Orienteering Challenge! A nice warm meal and hot sauna was surely awaiting them after finishing the race, so all was good in the end! The event in its main purpose was great. We accomplished to start a reseller journey together with people all the way from Tampere, Finland to the Netherlands and Japan!
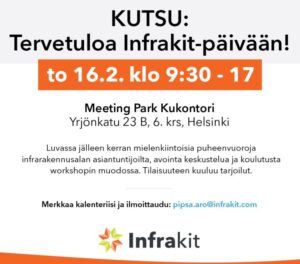
Infrakit Day 2017 invitation
Now we have come a full circle as Infrakit Day Helsinki is going to be held again soon, 16th of February! Again around 50 people is expected, and there is some room still left. Be fast and get a seat for you and your colleague from here: Infrakit Day 2017! Event is in Finnish, free of charge, and there is plenty of delicious food served – amongst our wonderful speakers, of course!
EDIT. The event was great, room filled with infra industry’s top people: read the blog post about it (in FIN) here.
Hope to see you in our events in 2017!
Book a Demo
Discover how Infrakit connects your entire infra project operations and drives value to every part of your business.
Recent Comments